When it comes to the integrity and performance of industrial equipment, particularly in the automotive and manufacturing industries, one of the most significant issues that can arise is pitting. The DEKRA VT1000 is a powerful tool designed to detect pitting and other surface imperfections. In this article, we will explore the importance of DEKRA VT1000 pitting images, how to identify pitting using this tool, and what steps you can take to prevent or manage it. Whether you’re a maintenance manager, mechanic, or simply an industrial equipment owner, understanding DEKRA VT1000 pitting images is essential for maintaining high operational standards.
What is Pitting, and Why is it a Concern?
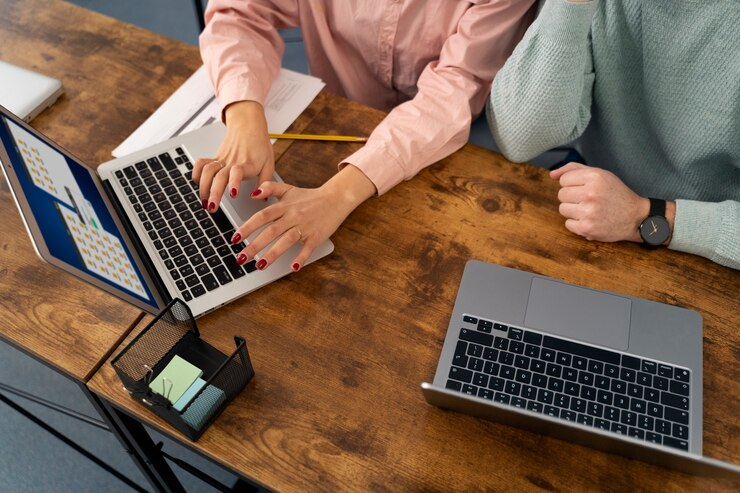
Pitting refers to the formation of small, localized pits or craters on the surface of materials, typically metals. These pits are caused by various forms of mechanical wear, chemical corrosion, or fatigue, and they can compromise the structural integrity of a material or component. In industries where precision and safety are paramount, such as in automotive or heavy machinery, pitting can lead to catastrophic failure if left undetected or unaddressed.
Some of the common causes of pitting include:
- Corrosion: Chemical reactions with the environment, such as exposure to moisture or harsh chemicals, can cause metals to corrode and form pits.
- Fatigue: Repeated mechanical stress over time can result in microfractures and pits forming on the surface.
- Manufacturing defects: Sometimes, pitting can arise due to defects in the material during production.
- Contaminants: Small particles or abrasive materials can cause wear on surfaces, resulting in pits.
Detecting pitting early is crucial to avoid more extensive damage or failure. The DEKRA VT1000 is a powerful tool in identifying pitting, and the images it produces play an essential role in early detection and diagnosis.
Understanding the DEKRA VT1000
The DEKRA VT1000 is a versatile, high-precision device used primarily for the inspection and evaluation of material surfaces. It uses advanced imaging technologies, including ultrasonic testing, to identify pitting, cracks, and other surface defects. The VT1000 is known for its accuracy, reliability, and ability to detect issues that may be invisible to the naked eye.
Here are some key features of the DEKRA VT1000:
- Non-destructive testing (NDT): The VT1000 allows for thorough inspection without causing damage to the material, making it ideal for ongoing maintenance of expensive equipment.
- High-resolution imaging: The device captures detailed images of the material surface, enabling users to identify even the smallest pits or cracks.
- Versatility: The VT1000 can be used on a wide range of materials, including metals, alloys, and composites, making it suitable for a variety of industries.
- User-friendly interface: The DEKRA VT1000 is designed to be intuitive, so even individuals with limited technical expertise can interpret the results effectively.
With these capabilities, the VT1000 provides valuable pitting images that help engineers and technicians detect issues early on, reducing downtime and preventing catastrophic failures.
How DEKRA VT1000 Pitting Images Help in Maintenance
The key to managing pitting and preventing damage is early detection. DEKRA VT1000 pitting images serve as a powerful tool in this regard. These images allow for a detailed visual assessment of the material’s surface, making it easier to spot even the smallest pits. By regularly inspecting surfaces using the DEKRA VT1000, maintenance teams can identify wear patterns, areas of stress concentration, and other issues that may lead to pitting.
Here’s how the pitting images from the DEKRA VT1000 help:
1. Early Detection of Surface Defects
Pitting typically begins as a small, almost imperceptible flaw. Without the right tools, these tiny defects can go unnoticed until they cause more severe damage. The DEKRA VT1000’s high-resolution imaging capabilities capture these early signs of pitting, which can be difficult to detect using conventional methods.
2. Accurate Diagnosis of the Extent of Damage
Once pitting has been detected, it’s crucial to assess how far it has spread. The DEKRA VT1000 pitting images provide a detailed view of the affected area, allowing technicians to measure the size, depth, and distribution of the pits. This level of detail aids in determining whether repairs are needed or if the component needs to be replaced.
3. Monitoring and Tracking Over Time
Pitting is a gradual process that can worsen over time. By regularly using the DEKRA VT1000, operators can track the progression of pitting on critical surfaces. By comparing pitting images over time, they can determine whether the situation is improving, stable, or worsening, helping them make informed decisions about maintenance schedules and interventions.
4. Improved Decision-Making for Repairs and Replacements
The detailed pitting images allow maintenance teams to make more informed decisions about whether a component can be repaired or if replacement is necessary. This helps reduce unnecessary replacements, saving costs, while also preventing more significant issues down the line.
How to Read DEKRA VT1000 Pitting Images
Reading pitting images from the DEKRA VT1000 may seem challenging at first, but with some understanding, it becomes easier to assess the severity of the issue. Here are some steps to guide you in interpreting DEKRA VT1000 pitting images:
Step 1: Look for Areas of Contrast
Pitting often appears as small, dark spots against the lighter background of the surface. These spots may vary in size and shape, depending on the depth and severity of the pit. The more contrast there is between the pit and the surrounding material, the easier it is to detect.
Step 2: Assess the Size and Distribution
Pay attention to the size of the pits and their distribution across the surface. Small, isolated pits may not be as concerning as large, widespread pitting, which may compromise the structural integrity of the material. If the pits are clustered in a specific area, it could indicate a localized stress point or weakness.
Step 3: Evaluate Depth and Penetration
The DEKRA VT1000 provides 3D imaging data, allowing you to assess not just the surface but also the depth of the pits. Deeper pits may indicate more significant damage, and if they penetrate beyond the surface layer, they could impact the component’s performance and lifespan.
Step 4: Check for Cracking or Spreading
In some cases, pitting may be accompanied by cracks or fissures. This is a more severe form of damage that requires immediate attention. If the pitting images show signs of spreading or cracking, it may be time to take action to prevent further deterioration.
Preventing Pitting: Tips and Best Practices
While DEKRA VT1000 pitting images are invaluable in detecting and diagnosing pitting, it’s also essential to take steps to prevent pitting from occurring in the first place. Here are some effective strategies:
1. Regular Maintenance and Inspections
Routine maintenance and inspections are key to preventing pitting. Using the DEKRA VT1000 to regularly check critical components for surface imperfections can help detect potential issues early. This proactive approach will allow you to address wear and tear before it turns into a major problem.
2. Proper Lubrication
Many instances of pitting are caused by insufficient lubrication, which leads to metal-on-metal contact and wear. Ensure that moving parts are properly lubricated to reduce friction and wear on surfaces.
3. Avoid Corrosive Environments
Exposure to harsh chemicals, moisture, and other corrosive elements can accelerate the pitting process. Whenever possible, protect equipment from these elements or use materials that are resistant to corrosion.
4. Implement Load Management
Excessive loads or repetitive stress can contribute to pitting. By managing the load on equipment and avoiding overuse, you can reduce the likelihood of fatigue-related pitting.
5. Use High-Quality Materials
Investing in high-quality materials with better resistance to wear and corrosion will help reduce the risk of pitting. Materials with higher tensile strength and fatigue resistance are less likely to experience pitting under normal operating conditions.
Conclusion
DEKRA VT1000 pitting images are an essential tool for identifying surface imperfections early, helping maintenance teams prevent more severe damage and costly repairs. By regularly using the VT1000 for inspections, operators can track the progression of pitting and take timely actions to mitigate its impact on equipment performance. With the right preventive measures in place and a keen eye for interpreting DEKRA VT1000 pitting images, you can ensure that your machinery and equipment remain in top condition, minimizing downtime and extending their service life.